Our Process
Watch the video as we transform raw stone into natural stone veneer at our Sturgeon Bay facility.
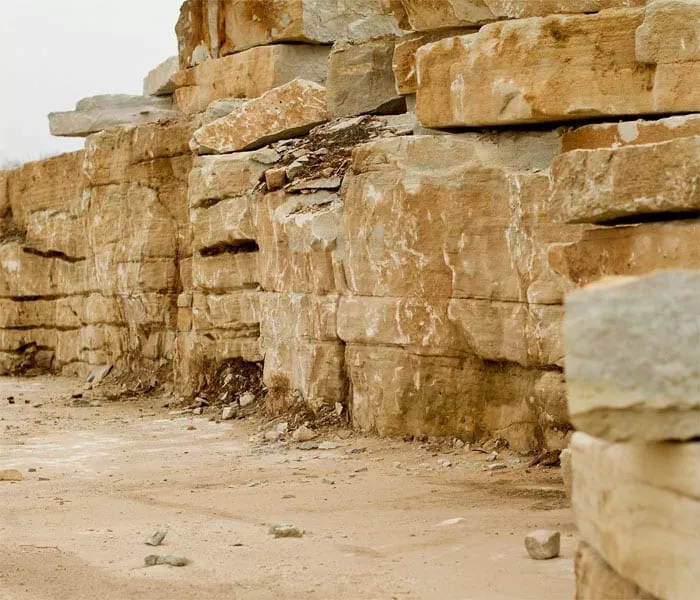
STEP 1
Stone Quarrying
Our stone is quarried in ledges that are roughly five feet high. In this image, you can see an example of a fissure, or a crack in the ground. Fissures like these allow minerals to seep into the ground, giving the stone its unique color and texture.
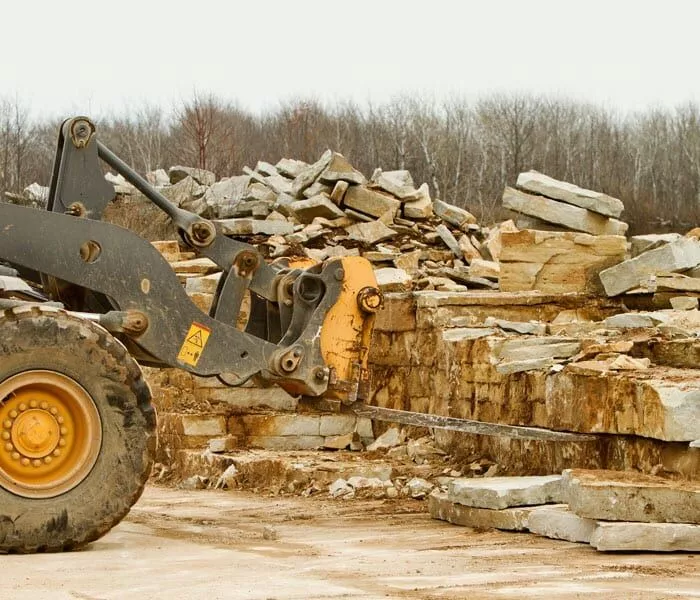
STEP 2
Stone Extraction
A loader extracts the stone slabs from the quarry by popping up the layers, one at a time. The stone comes out in sheets of varying sizes and thicknesses, which allows us to offer a variety of final products.
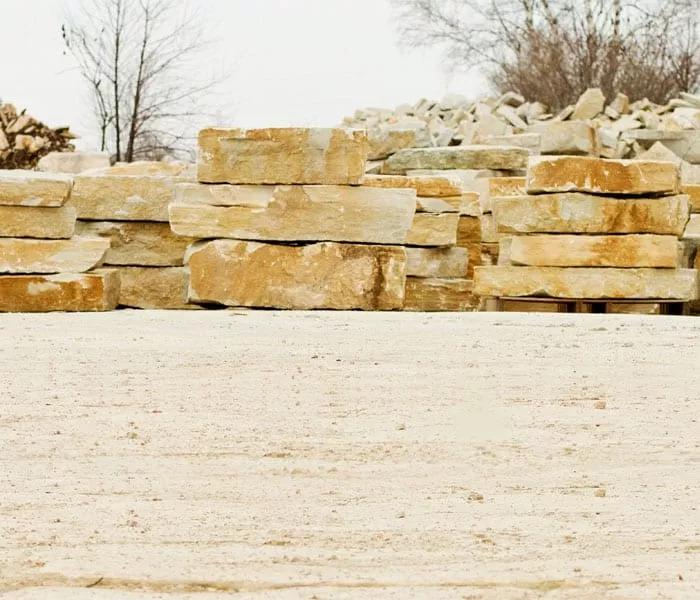
STEP 3
Stone Sorting
The stone is sorted based on three characteristics: color, size, and thickness. Based on these attributes, we decide which product the stone’s meant to become. Most stones are destined for the cut shop, while others are reserved as landscape outcroppings, which are sold in their natural state. This is the first step in our rigid quality control process. Pieces that don’t make the cut simply do not make it beyond this step.
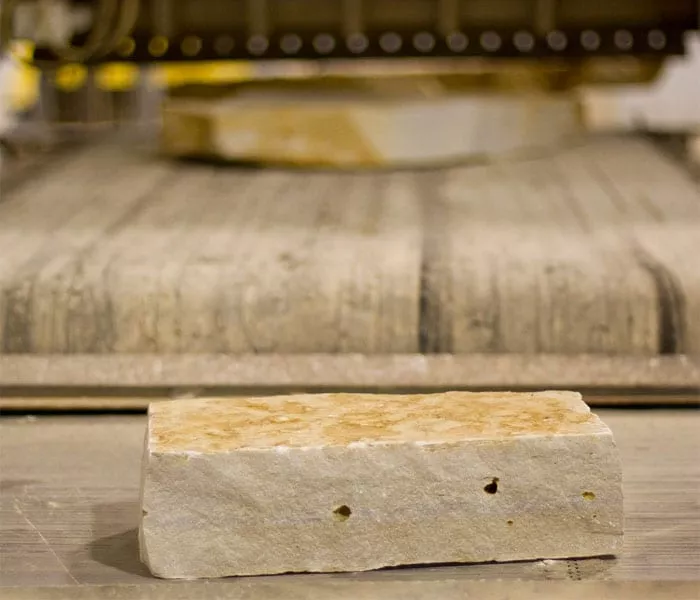
STEP 4
Stone Splitting
Slabs of stone are brought into the manufacturing facility (aka the cut shop) to be cut by the splitter. The splitter is a large hydraulic press that breaks the stone sheets into pieces of the desired sizes and shapes. (While we’re talking shop: this process is also sometimes called snapping, chopping, or machine cutting.) After the initial cut, we also use the splitter to trim any rough edges and perform basic touch ups, in preparation for the quality check process.
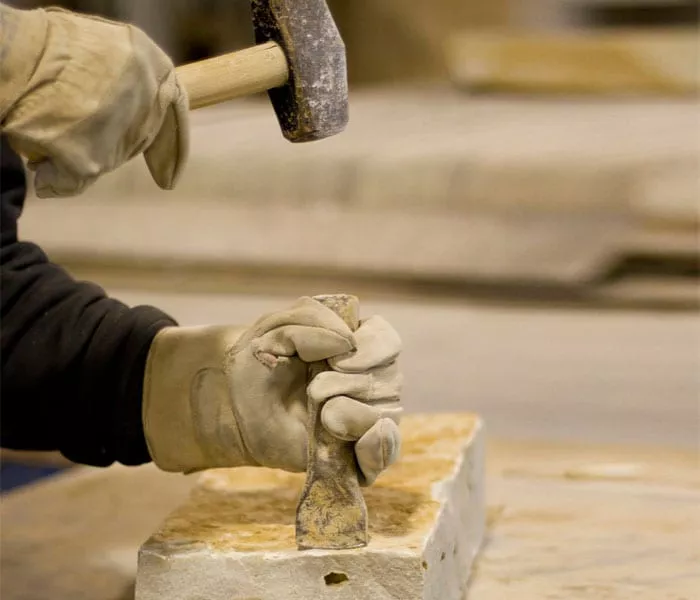
STEP 5
Quality Check
The stone is given a visual inspection, and any imperfections are removed by hand. Our careful and thorough quality control process ensures a cleaner, more consistent stone that is easier to install.
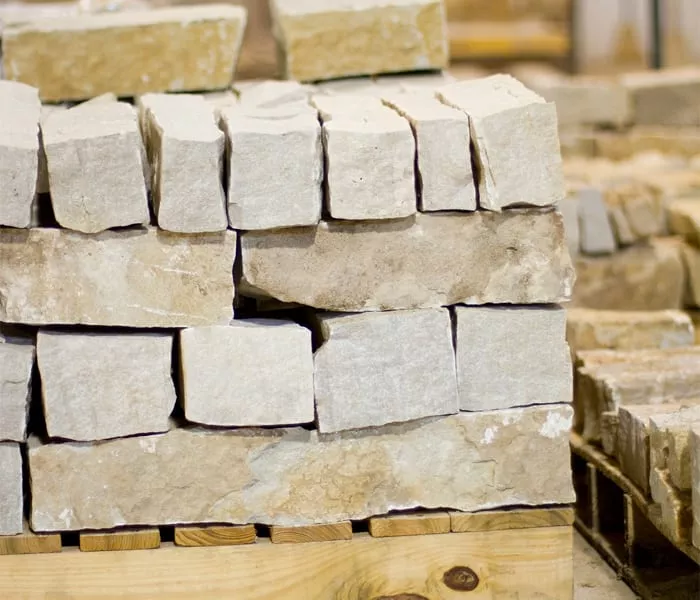
STEP 6
Product Separation
At this point in the process, the cut pieces are sorted to be sawn into their respective products.
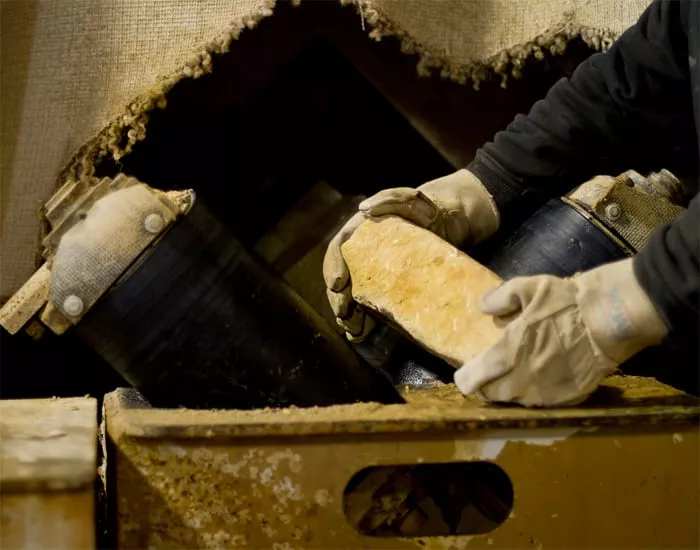
STEP 7
Thin Veneer Cutting
Stone that will become thin veneer is carefully loaded into the saw by hand. This process is performed only by our most experienced staff, who are well trained in safety measures and in the methods of properly sawing thin veneer stone to a consistent thickness.
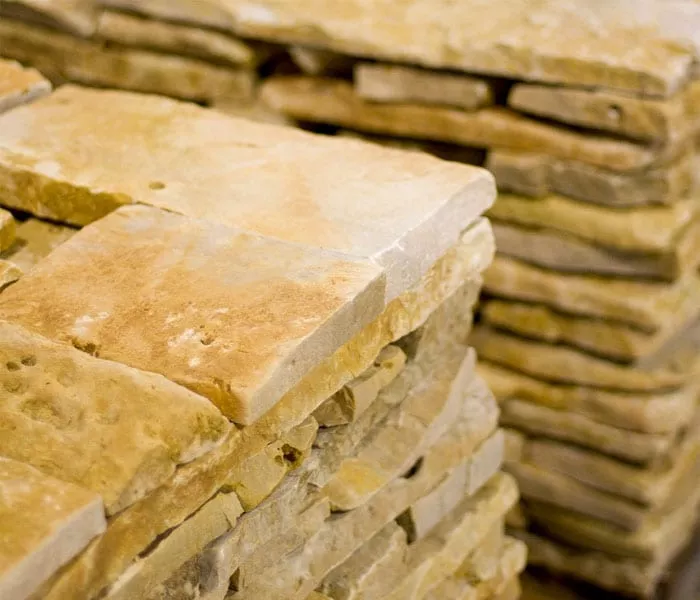
STEP 8
Delivery
The finished stone is neatly stacked on pallets and prepared for delivery. Now, just one question for you: where to?